塗工方法の選択、粘度調整、ゲルタイムの把握まで、一貫したSolutionを提案
当社は、接着剤塗工方法の選択、粘度調整、硬化時間(ゲルタイム)の把握まで、一貫したSolutionを提案いたします。
塗工方法選択におけるSolution
枚葉塗工における最適な塗工方法の選定
バーコーター、アプリケーター、グラビア、フレキソ(グラビアオフセット)など、
材料の粘度や、目標とする塗膜厚に応じて最適な塗工方法を初期選定が可能です。
塗工方式 |
Wet膜厚 |
メリット |
デメリット |
枚葉 |
R2R |
|
|
|
バーコーター |
バーコーター |
1.5~500μm |
再現性が高く、細かな厚み変更が容易 |
塗工後のレベリングを利用するため、高粘度液体ではスジが残る
バーが基材に直接接触するため、コンタミ混入や基材傷の可能性あり |
アプリケーター |
ナイフオーバーロール
コンマコーター
ダイコート |
数10μm |
後計量方式で高粘度液体に適する |
ギャップ設定で厚み精度が決まる
基材の平坦性に影響を受けやすい
ラインスピードを上げにくい |
グラビア |
ダイレクトグラビア
リバースグラビア
小径グラビア等 |
約1~20μm |
薄膜、R2Rへの安定した塗工が可能 |
高粘度液体では凹版への抜けが起きる |
フレキソ(グラビアオフセット) |
グラビアオフセット
差動グラビアオフセット(加温)等 |
約0.5~10μm |
薄膜アプローチ・水性塗工液への展開可能 |
ゴムローラー使用による溶剤制限あり
耐久性の課題 |
K303Sマルチコーター
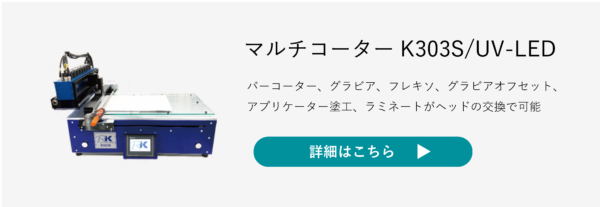
バーコーター/ アプリケーター/ グラビア/フレキソ/ ラミネートの印刷・塗工方式に対応
・A3 サイズまでのサンプルを手軽に作成
・UV-LED照射器が搭載可能!印刷、塗工後直ぐにUV照射ができます
・少量の材料で的確な試験が可能
・印刷、塗工スピード設定40m/min
・人的誤差を無くした再現性ある試験が可能
R2Rパイロットコーターで塗工条件、乾燥(硬化)条件の決定
R2Rパイロットコーターでは、枚葉式では困難な塗工条件、乾燥・硬化条件の最適化が可能です。枚葉式で得られた塗工方法や粘度のデータを基に、ライン速度、乾燥・硬化温度などを細かく調整し、量産に近い条件での検証が行えます。さらに、保護フィルム(セパレーター)との貼り合わせサンプルも作成できます。
ラボ/パイロットコーター VCML
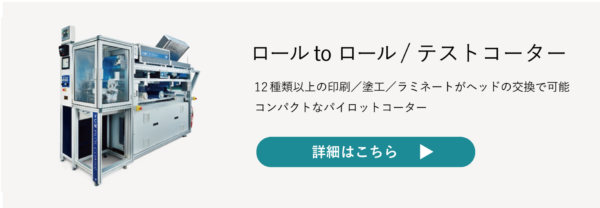
12種類以上の印刷、塗工が選択可能 オプションでUV(ランプ、LED)が可能
生産機との相関が取れる試験ができ、材料開発/ サンプル作製/ 量産前試験/ 生産現場で発生した不具合の検証などのスピードアップ、コストダウンを実現します。
・印刷、塗工
フレキソ印刷 /グラビア印刷 / ロータリースクリーン印刷 / ダイレクトグラビア /
リバースグラビア / 小径グラビア/ オフセットグラビア / メーターバー / ナイフオーバーロール /
コンマ・バー / 差動オフセットグラビア/ エアナイフ / スロット・ダイ 他
・オプション
UV(ランプ、LED)※窒素パージ選択可、コロナ処理、熱風乾燥、IR乾燥、加熱ラミネーター、電気テンション制御、エッジガイドetc
塗工液の材料設計、物性の把握におけるSolution
粘度、レオロジー、硬化温度、硬化時間(ゲルタイム)、ポットライフの測定
乾燥条件、硬化条件を検討するためには正確な硬化時間(ゲルタイム)の把握が不可欠です。
またポットライフの把握は生産性、品質管理において重要です。ゲルタイムを自動測定装置は、樹脂の硬化挙動をグラフで可視化します。
ゲルタイム測定装置 まどか
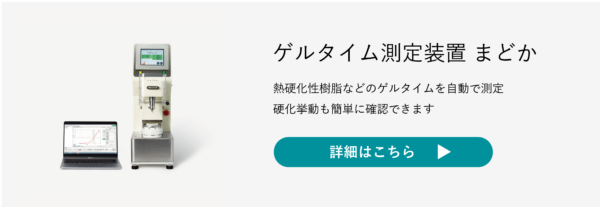
・様々な樹脂のゲルタイムが測定可能
熱硬化性樹脂、2液硬化型樹脂、湿気硬化型樹脂、常温硬化型樹脂など
エポキシ、シリコーン、ウレタン、フェノール、不飽和ポリエステル、PVC、フラン樹脂、アクリル樹脂
・ユーザー例
プリプレグ、半導体封止材、接着剤、粘着剤、摩擦材、シーリング材、塗料他
・統計データから管理図、ヒストグラム図、パレート図を簡単に作成できます
新型ゲルタイム測定装置しずか
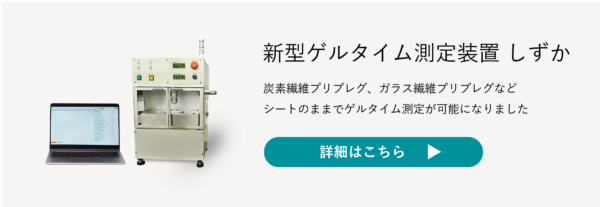
・カーボンプリプレグなどシート状のままゲルタイムを測定。様々な樹脂の測定が可能
クロス(織物プリプレグ)、UD(一方向タイプ)、トウプリプレグ
ガラス繊維プリプレグ、RCC(樹脂付銅箔)、SMC(Sheet Molding Compound)、
エポキシ、フェノール、不飽和ポリエステル、ウレタンなど
・10μmの 極薄プリプレグから厚みのある材料まで測定が可能
・温度条件として、一定温度、昇温での測定が可能
熱板温度を一定にした状態で試料を投入し測定することも、昇温させながら測定することも可能
・液体& 粉体サンプルの測定
高充填フィラー入りサンプル、嫌気性サンプル、ゼリー状サンプルなど幅広く対応
・硬化挙動をグラフで可視化
判定値(閾値)を設定し、ゲルタイムを自動計算します。
また、測定したせん断応力から、粘度、位相、せん断弾性率などを計算しグラフ化します。
松尾産業では、接着剤の塗工方法選択から粘度・レオロジーの調整、硬化時間(ゲルタイム)の測定まで、一貫したプロセスで最適なソリューションをご提案いたします。
新横浜駅から徒歩5分のデモルームにてテスト受付中!
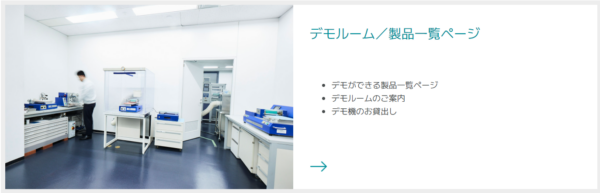
新横浜駅から徒歩5分のデモルームにて、各種試験や最適条件の検証が可能です!サンプルをお持ちいただければ、実機での塗工・硬化テストを通じて、量産に向けた最適なプロセスをその場で確認できます。
松尾産業の〝ウェットコーティングSolution”〝熱Solution”デモルームに是非お越しください。
▼お問い合わせはこちら
▼カタログダウンロードはこちら